Several applications with servo position control can be replaced with inverter having special software and motor with encoder, giving a major cost saving.
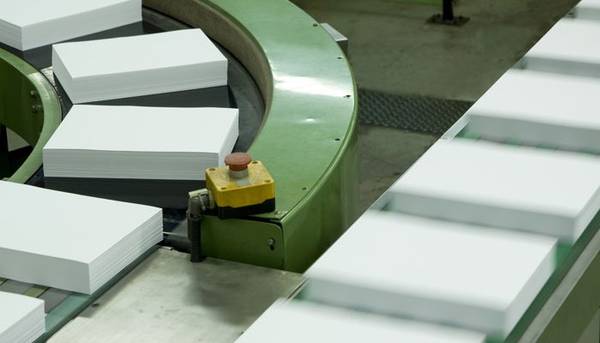
- Three Positioning TypesLinear AxisAbsolute and Relative MotionManual Operation (Jog Forward / Reverse).
- Positioning Quantity SourceSelection by Parameters, directly selected by D/IsRS232/485/422 Modbus RTUField Bus Option (CANopen or other field bus protocols).
- Distance Format Setup (User Units)Use of Signed or Unsigned Position Values16- or 32- Bit Position Reference Mode for High Dynamic RangeDistance in Millimeter (mm), Centimeter (cm), Meter (m), Degree (°), or Revolution (rev) UnitsUser-Defined Distance Format (Number of Digits and Decimal Places)
- Reference Switch SearchSearch Sequences for Hardware Limit Switches (3 different switches)Home Offset Value Set as 0-Position or Driven from 0-Position3 Different Speeds During Reference Search for High Accuracy.
- Position LimitsBy Hardware and Software,Changeable during Positioning.
- Encoder SupportPGB3, PGX3 (sincos, incremental).
- Brake ControlBrake Sequence similar to L1000A Elevator Brake ControlMove Command Delay TimeBrake Open and Close Delay TimeOutput Contactor Control including Response Signal and Open Delay Time.
- Status MonitorsDistance from 0-PositionCommanded Position, Speed, Ramp TimeDistance to GoPosition ErrorRaw PG PulsesMotor Shaft Angular RotationZ-Pulse Monitor.
- Status SignalsIn-Position, Zone Signal, Reference Search Ready, “Zone” Signal, Motion Control Disable.
- Faults and AlarmsHardware / Software LimitPositioning Setup Error (detects wrong setup configurations)Positioning Error (Position not reached in expected time)Reference Search Error (Expected hardware switch could not be found) Emergency Stop Alarm (After sequence abortion).